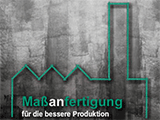
Seit Ende 2009 kämpft Deutschland mit den Nachwehen der größten Wirtschafts- und Finanzkrise der Nachkriegszeit. Viele produzierende Unternehmen versuchen, selbst in diesen Zeiten Chancen zu realisieren, indem sie betriebliche Abläufe überprüfen und Optimierungspotenziale aufdecken. Das Fraunhofer IAO hat jetzt in einer Studie unter mehr als 300 produzierenden Unternehmen die dazu notwendigen Methoden unter die Lupe genommen und Stärken und Schwächen ermittelt. Besonders für die klassische Wertstromanalyse scheint die Zeit für einen Neuanfang gekommen.
Klassische Wertstromanalyse: Populär trotz klarer Grenzen
In der Industrie kommt eine Vielzahl von Methoden unterschiedlichster Komplexität zum Einsatz. Die Wertstrommethode dient als Klammer über mehrere Methoden aus dem Lean-Baukasten und belegt mit einer Anwenderquote von rund 60 Prozent einen Platz in den vorderen Rängen. Wertstromexperten gelingt es, Bestände und Durchlaufzeiten um mehr als 30 Prozent zu verringern und die Produktivität um mehr als 20 Prozent zu steigern. Kein Wunder also, dass acht von zehn Unternehmen angeben, mit der Wertstrommethode und ihren Ergebnissen zufrieden zu sein. Tatsächlich bietet die Wertstromanalyse klare Vorteile bei der Prozessdarstellung. Sie vereinfacht komplexe Prozesse und hilft gerade bei Produktionsprozessen der Serienfertigung, Potenziale zu erkennen. Doch diese Fokussierung ist auch eine Schwäche, wie unsere Studie zeigt.
Klassischer Wertstrom und der Teufel im Detail
Mehr als die Hälfte der Befragten sieht auch nach einer Wertstromanalyse weiteres Potenzial in der Organisation ihrer Produktion. Dies zeigt, dass nicht alle Problemstellungen mit den bisherigen Wertstromansätzen gelöst werden können. Wertstrom wird besonders selten von Einzel- und Kleinserienfertigern verwendet, die auch deutlich schlechtere Ergebnisse in der Anwendung erzielen. Wertstromdesign kann also seine Stärken nicht entfalten, sobald die Rahmenbedingungen der Serienproduktion verlassen werden – und das ist bei vielen Unternehmen des produzierenden Gewerbes der Fall. Ursprünglich kommt die Wertstrommethode aus der Automobilindustrie, wo mit vergleichsweise großen Stückzahlen und einheitlichen Produktionsabläufen jedoch andere Rahmenbedingungen herrschen als beispielsweise im Maschinen- und Anlagenbau. Hier dominiert eine Vielzahl verschiedener Typen und Varianten, die zu kleinen Serien und produktspezifischen Produktionsabläufen führt. Doch je komplexer die Abläufe und je heterogener die innerbetrieblichen Strukturen, desto geringer die Erfolgschancen der klassischen Wertstromanalyse.
Wertstrom-Engineering – Maßanfertigung für die bessere Produktion
Das Fraunhofer IAO entwickelt die bislang bekannte Wertstrommethodik kontinuierlich weiter, um diese Defizite durch gezielte Erweiterungen und methodische Innovationen auszugleichen. Der Schlüssel zum Erfolg des »Wertstrom-Engineerings« liegt unter anderem in der Betrachtung des vollständigen Wertstroms. Das methodische Einbeziehen des gesamten betrieblichen Umfelds, über den Vertrieb, die Konfiguration und Disposition bis zur Produktion erlaubt es, vollständige betriebliche Prozesse abzubilden.
Darüber hinaus verlangen gerade kundenindividuelle Produkte des mittelständischen Maschinenbaus einen neuen, vertieften Blick in die Details der Produktion. Die neuartige Symbolik des »Wertstrom-Engineerings« setzt genau hier an. Mit ihrer Hilfe ist es möglich, selbst bei Produktionen mit geringen Stückzahlen und einer Vielzahl unterschiedlicher Abläufe Optimierungspotenziale zu erkennen. Die Leitgedanken, Methoden und Hilfsmittel zur erfolgreichen Verbesserung von Abläufen – insbesondere für die typen- und variantenreiche Produktion – stellt das Seminar »Wertstrom Engineering« Mitte Juni 2010 vor. Wenn Sie wissen möchten, wie Sie das Methodenset für den Erfolg Ihres Betriebs einsetzen können, laden wir Sie herzlich ein, an unserem Seminar teilzunehmen. Die aktuelle Studie »Wertschöpfung steigern« fasst die Ergebnisse der Unternehmensbefragung zusammen und ist ab sofort im IAO-Shop erhältlich.
Kategorien: Advanced Systems Engineering (ASE)
Tags: Produktion, Produktionsmanagement