Die Elektrifizierung und Abkehr von fossilen Brennstoffen verspricht Klimaschutz und Energieunabhängigkeit – aber sie hat eine gravierende Kehrseite, die noch zu wenig beachtet wird: Die Herstellung der dafür nötigen Lithium-Ionen-Batterien vom Abbau der Rohstoffe, über die energieaufwändige Produktion bis hin zur Entsorgung, bringt signifikante ökologische und soziale Auswirkungen mit sich. Laut Global E-Waste Monitor 2020, einer Studie der Vereinten Nationen (UN), wurden im Jahr 2019 weltweit etwa 53,6 Millionen Tonnen Elektroschrott erzeugt. Batterien haben einen erheblichen Anteil daran. Eine klima- und umweltgerechtere Lösung könnten mechanische Speicher sein, deren Vorläufer bereits im Mittelalter entwickelt wurden.
Die grundlegende Idee für derartige Energiespeicher ist keine neue: schon ab dem 15. Jahrhundert wurden Federn dazu genutzt, um Energie für eine Vielzahl von Gerätschaften zu speichern, von mechanischen Uhren bis hin zu Industriemaschinen. Moderne Uhrwerke verwenden eine Kombination aus Energiespeicher, Gehwerk, Schwingsystem und Zeigerwerk, um die in der Feder gespeicherte Energie in kleinen Impulsen über mehrere Tage hinweg langsam abzugeben. Mit dem Fortschritt der technologischen Entwicklung stießen diese Anwendungen jedoch an eine physikalische Grenze. Auf ihre Masse bezogen können moderne Lithium-Ionen-Akkus in etwa das 10.000-fache an Energie speichern wie eine Drehfeder. Zudem kann diese Energie effizient und gleichmäßig in Form von Elektrizität zur Verfügung gestellt werden. Das ist der Grund, weshalb wir in unserem Alltag (noch) keine federbetriebenen Smartphones oder Pkw sehen. Wann immer es darum geht, vergleichsweise große Mengen an elektrischer Energie in kompakter Weise zur Verfügung zu stellen, sind Batterien und Akkus nicht zu schlagen. Doch auch mechanische Federn haben ihre Stärken:
- Autonomität: Mechanische Energiespeicher lassen sich auf mechanische Weise laden und sind somit nicht vom Stromnetz abhängig.
- Verfügbarkeit: Federbasierte mechanische Energiespeicher bestehen aus Federstahl und benötigen somit ausschließlich Materialien, welche in Deutschland erzeugt werden können. Es besteht keine Abhängigkeit von internationalen Lieferketten, welche sich im Zuge der COViD19-Pandemie, von Handelskonflikten und des Ukrainekriegs für viele Unternehmen als wenig resilient erwiesen haben.
- Umweltverträglichkeit: Der Beitrag zur Nachhaltigkeit besteht vor allem in signifikant geringeren Energieaufwänden in der Fertigung und deutlich besserer Recyclingfähigkeit.
- Robustheit und Sicherheit: Sekundärbatterien verlieren nach einigen hundert oder tausend Ladezyklen signifikant an Funktionsfähigkeit, während mit Drehfedern viele Millionen Ladezyklen möglich sind. Zudem können bereits geringe Schäden an Akkus zur Selbstentzündung führen, wie einige spektakuläre Brände von Elektroautos demonstrierten.
Einzelne Anwendungen auf dem Markt, wie kurbelbetriebene Notlampen machen sich diese Eigenschaften bereits zunutze, um kleine Marktnischen zu bedienen. Um elektrischen Energiespeichern wie Batterien und Akkus die Stirn bieten zu können, müssten also Anwendungen gefunden werden, bei denen die Stärken federmechanischer Energiespeicher besonders zum Tragen kommen und die intrinsischen Schwächen von geringerer Bedeutung sind. Zudem muss der Entwicklungsvorsprung ausgeglichen werden, welcher sich durch die gezielte Investition in elektrische Energiespeicher über die letzten Jahrzehnte hinweg aufgetan hat: Lithium-Ionen-Akkus sind inzwischen Standardkomponenten, welche sich problemlos in die verschiedensten Geräte integrieren lassen. Dies spart Kosten entlang des Produktlebenszyklus und hebt jeglichen ökonomischen Vorteil durch geringere Materialkosten auf. Durch die Standardisierung können Lithium-Ionen-Akkus in großen Stückzahlen gefertigt werden. Etwas Ähnliches müsste für federmechanische Energiespeicher geschehen, wenn diese mit der Konkurrenz mithalten möchten.
In dem Projekt FeMecEs4.0 untersucht das Fraunhofer IAO gemeinsam mit dem Federnhersteller Haller-Jauch die Möglichkeit, einen derartigen Feder-Mechanischen Energiespeicher zu entwickeln und herzustellen. Er soll Teil eines standardisierten Powerpacks sein, welcher alle Komponenten umfasst, welche für die Substitution elektrischer Energiespeicher nötig sind. Im Laufe des Projektes sind dementsprechend bereits mehrere Demonstratoren entwickelt worden, welche dieses Wirkprinzip abbilden.
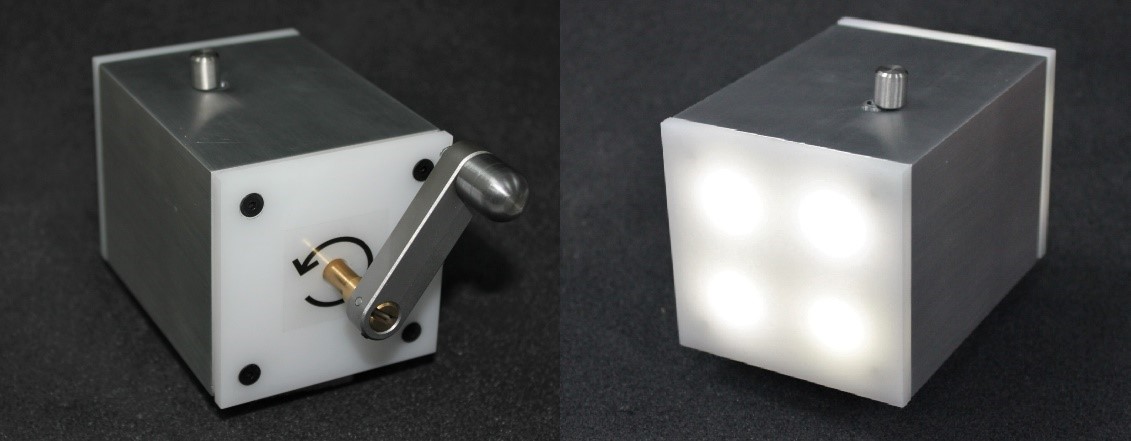
Abbildung 1: Dritter Demonstrator eines federbasierten mechanischen Energiespeichers aus dem Projekt FeMecEs4.0 (Quelle: Haller-Jauch)
Wie auf Abbildung 1 zu sehen ist, besteht der Demonstrator aus einem federmechanischen Energiespeicher, welcher von einer Kurbel aufgezogen und somit »geladen« werden kann. Sobald der Schalter auf der Oberseite des Demonstrators betätigt wird, beginnt sich die Feder zu entspannen und gibt Energie in Form einer langsamen Drehung ab. Diese Bewegung wird dann in eine Rotation mit ausreichender Geschwindigkeit umgewandelt, um einen Generator anzutreiben, welcher daraus elektrischen Strom generiert. Von diesem Strom werden vier LEDs betrieben. Die größte Herausforderung besteht hierbei darin, die nicht unerhebliche Menge an mechanisch gespeicherter Energie kontinuierlich und kontrolliert abzugeben und umzuwandeln: Der erste Demonstrator erzeugte tatsächlich 40-mal so viel Strom wie benötigt, jedoch nur für einige Minuten. Derzeitige und künftige Entwicklungsbemühungen konzentrieren sich daher darauf, die Anforderungen moderner elektronischer Geräte und deren verschiedene Anwendungsszenarien erfüllen zu können. Gleichzeitig sollen die Umweltauswirkungen des neuen Powerpacks über den gesamten Produktlebenszyklus hinweg – von der Produktion bis zum Recycling – so gering wie möglich gehalten werden.
Denn darum soll es am Ende gehen: Die gewohnte Qualität einer batteriegestützten Energieversorgung kombiniert mit der Robustheit und Nachhaltigkeit recyclebarer Komponenten. Ob sich alle technischen Herausforderungen an diese neue (alte) Technologie überwinden lassen, wird sich in den nächsten Monaten zeigen. Vielleicht sehen wir schon in naher Zukunft einige Produkte von Nachtischleuchten bis hin zu Messgeräten, welche statt eines Akkus eine Drehfeder enthalten. Wir sind gespannt.
Leselinks:
- News 23.4.2024: Ersetzt moderne Federtechnologie Akkus und Batterien?
- Kostenloser Leitfaden für eine ressourcenschonende smarte Produktentstehung
- Uhr mit Federantrieb – 1430
Kategorien: Nachhaltigkeit
Tags: Industrie 4.0, Produktion
Wir kennen doch diese mechanische Speicherung doch von den Kinderspielzeugen. Die dort meist verwendete Stahlfeder könnte sich doch auch mit anderen Materialien ersetzt werden. Vielleicht auch mit einem Art Druckmechanismus. Gewichtsmäßig sind diese Möglichkeiten gegenüber Akkus möglicherweise vorteilhafter
Auf Ihre homepage bin ich aus folgendem Grund gestoßen, da ich eine Frage habe:
Ein Speicherwerk in einem Spiralfederwerk könnte über Monate die überschüssige Energie aus einer Photovoltaikanlage aufnehmen und sie dann im Bedarfszeiten(Winter) laufend an Batterien oder direkt abgeben? Könnte man solche Federwerke in Serie schalten?
Vielen Dank für Ihre Interessenahme!
Hallo Herr Toll,
Auch wenn Ihr Vorschlag für den Sonderfall eines Spiralfederwerks möglich ist, würde es sich wirtschaftlich vermutlich nicht lohnen. Im Vergleich zu Lithium-Ionen Akkus lässt sich in Federn nicht genug Energie speichern, um den Aufwand zu rechtfertigen. Das ist leider ein rein physikalisches Limit – unabhängig von der Effizienz der Umsetzung.
Ja, für den Sonderfall eines Spiralfederwerks würden die Investitionskosten für die Beschaffung von Spiralfedern entfallen.
Man müsste je nach Verfügbarkeit von überschüssiger Energie die gelagerten Federn aufziehen und bei Bedarf wieder entladen. Gleichzeitig müsste man jedoch im Auge behalten, wann die Federn für die Auslieferung an den Kunden benötigt werden – das ist nicht unbedingt immer miteinander zu vereinbaren. Die Menge an gespeicherter Energie rechtfertigt m.E. nicht den zusätzlichen (Personal-)Aufwand durch die komplexere Logistik. Es wäre in diesem Fall vermutlich einfacher, ins Netz einzuspeisen, auch wenn man dadurch ein wenig Potential verschwendet.
Insgesamt sehe ich Federn aufgrund des ungünstigen Verhältnisses von Energiespeicherkapazität zu Masse bzw. Volumen als Speichermedium für Überkapazitäten für ungeeignet – v.a. verglichen mit den Alternativen Pumpspeicherkraftwerk oder Wasserstoff.
Sehr geehrter Dr. Barwasser,
wie müsste eine Flach-Spiralfeder gebaut sein (Größe, Stärke ecc.), um 1 Kwh speichern zu können (rotierende Kraftzufuhr über Windkraft)?
Vielen Dank!
Das lässt sich nicht so einfach sagen, weil es mehrere Auslegungsgrößen gibt. Entscheidend sind
– die Anzahl der Wicklungen und damit der Auslenkungswinkel (um wie viele Umdrehungen kann ich die Feder aufziehen),
– das verwendete Material, insbesondere E-Modul
– die Dicke/Geometrie der einzelnen Wicklung –> zusammen mit E-Modul für die Steifigkeit verantwortlich
– der mittlere Durchmesser der Feder, sowie Hebelarm der Arbeitskraft und Gegenkraft.
Die Formeln finden Sie z.B. hier:
https://help.autodesk.com/view/INVNTOR/2024/DEU/?guid=GUID-ABAD1D28-C07E-48F3-9CEC-16CE9D5D2A52
In jedem Fall wird eine 1kWh Feder riesig sein.
Eine rein persönliche frage: Glauben sie, dass es diese Federn irgendwann als Akkus geben wird? Also nicht so als Handy akkus, sondern für den Hausgebrauch und ähnliches.
Wir arbeiten dran. Aktuell läuft ein Folgeprojekt „FECycle“, bei dem wir genau das erreichen wollen. Ich bin mir sicher, dass wir bis Ende des Jahres einen solchen „Akku“ entwickelt haben werden. Der aktuelle Prototyp kann schon viel mehr, als das, was ich hier vor einem Jahr vorgestellt habe. Dennoch bleiben einige harte Limits, was die Energiedichte einer mechanischen Feder vs eines Lithium-Ionen Akkus betrifft. Daher wird es immer bei einer Nischenanwendung bleiben. Am ehesten könnte ich mir vorstellen, das solche „Akkus“ in Regionen der Welt zum Einsatz kommen werden, in welchen es keinen verlässlichen Zugang zu einem Stromnetz gibt.
Sehr geehrter Dr. Barwasser,
Ich beschäftige mich derzeit aufgrund eines FH-Projektes mit federbasierten Energiespeichern und wollte daher wissen welche Abmessungen der FeMecEs4.0 hat und welche Leistung er dabei bereitstellen konnte und wie lange man dafür kurbeln musste. Bzw. wie viel Leistung mit dem neuen Projekt FECycle voraussichtlich bereitgestellt werden kann.
Vielen Dank!